Protein Supplement production in industrial sector – Part 6
Saturday, January 21st, 2012 4:04:12 by Ahmed Tariq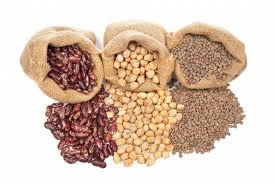
Protein Supplement production in industrial sector – Part 6
A fed-batch process offers a method to eliminate this production. If the concentration of the substrate is kept below 0.25 g/l then fermentative metabolism will be restricted (Daramola and Zampraka, 2008). This is achieved by the substrate being fed to the
reactor incrementally.
One advantage the fully batch process has is with regards to pumping. With the fed-batch system the substrate must be pumped to the fermentor vessel through out the process. As the biomass increases exponentially therefore the amount of substrate required
will also increase exponentially. There are two possible approaches to meeting this requirement.
Either the concentration of the feed substrate is kept constant and the flow rate is changed or the flow rate is kept constant and the concentration is altered. The most practical of these is to keep the concentration constant, as the substrate has already
been prepared with a certain concentration.
However, this means then that a pump must be used which can operate at the full range of the substrate feed rate required. This problem is not present in a full batch system as all of the substrate can be fed to the reactor at a constant rate at the start
of the fermentation and then it ceases.
Once the philosophy of the batch process is decided it is then crucial to consider how long the batch fermentation will last. This can depend on how the inoculum is prepared.
If the feed seed is placed in the fermentor at initial conditions the batch will have to be left for a longer period. This is due to the fact that the cells will go through the lag phase of growth in the fermentor, when no growth occurs due to the cells
acclimatising to the conditions of the fermentor.
It is common place however, to inoculate the feed seed. This means that the feed will be entering the fermentor already in the exponential phase. This lag effect can also be reduced by entering the feed in similar conditions to that of the fermentation,
i.e., same temperature, pH and pressure.
Once the fermentation has had any unnecessary time taken off the process a decision must be made on the full desired length of the fermentation period. The yeast will continue growing as long as the conditions are suitable.
This means that for longer batch times a greater percentage increase will be achieved for the initial feed yeast. This can be shown using an analytical solution of Pirt’s Law (Daramola and Zampraka, 2008).
With a base for the fermentor having to produce 9000kg per day and a specific growth rate of 0.215hr-1, therefore, with a batch time of 20 hours the initial feed would need to be 122kg.
This can then be compared with a batch time of 40 hours which gives an initial feed of 3.3kg. This means that for a 20 hour batch the process would require 1.35% of the final product amount for initial feed whereas for a 40 hour batch it is as low as 0.018%
for the feed.
Continued in part 7
Tags: 2011, 2012, Industrial, Jan Dawson, lahore, Nokia Developer Website, Nokia s new Lumia 900, production, Report, researchShort URL: https://www.newspakistan.pk/?p=10040