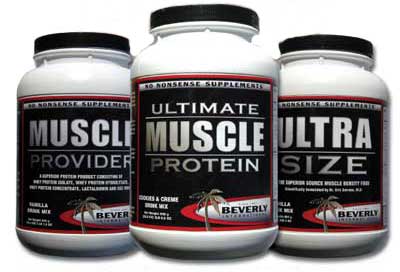
Protein supplement production process description – Part 1 In this section, details of the mass and energy balances along with the drying process description are detailed. Introduction Yeast broth from the fermentor is delivered to separator which produces a thick suspension of yeast (cream). Moisture in the cream needs to be evaporated to get the […]
Mar 6 2012 | Posted in
Sci-Tech |
Read More »
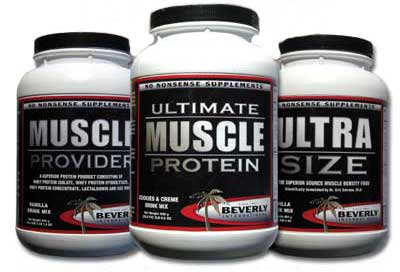
Separation of dried products from the air – Part 2 The discharge of the product from the drying chamber is called the primary discharge. The primary recovery of the product is from the conical base of the chamber due to the separation effect of the cyclonic air flow created within the cyclone. This guides the […]
Mar 5 2012 | Posted in
Sci-Tech |
Read More »
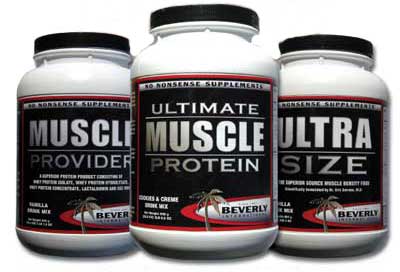
Separation of dried products from the air The fourth and the last stage of the spray drying process is the separation of the dried product from the air. The recovery of the product from the dryer is carried out in a two point discharge design. Primary separation of dried products takes place at the bottom […]
Mar 2 2012 | Posted in
Sci-Tech |
Read More »
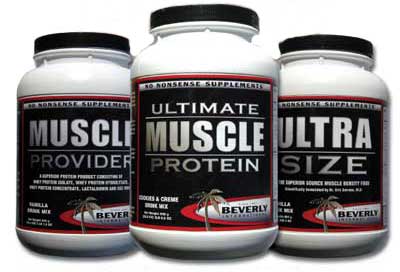
Sizing of a spray dryer – Industrial sector article The sizing of spray dryer on a purely thermal basis is a quite simple since the evaporation is entirely a function of the change in temperature across the dryer. The design of an efficient spray dryer requires considerable expertise along with large scale test facilities, particularly […]
Mar 1 2012 | Posted in
Sci-Tech |
Read More »
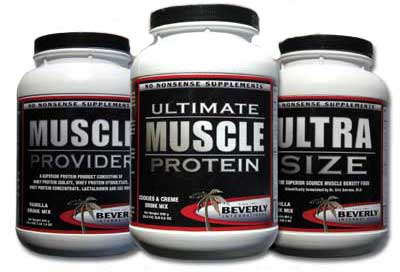
Designing of the dryer section of nutritional yeast production plant – Industrial sector review – Part 21 Drying of Spray When the spray comes into contact with the drying air, evaporation takes place from the ‘saturated vapor’ film which is established at the droplet surface. The surface temperature of the droplet approaches the wet bulb […]
Feb 29 2012 | Posted in
Sci-Tech |
Read More »
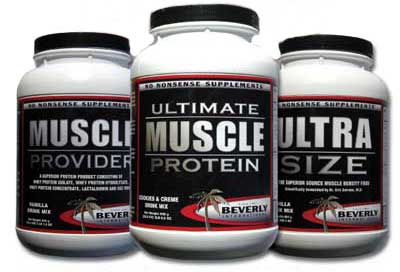
Designing of the dryer section of nutritional yeast production plant – Industrial sector review – Part 20 Spray-air contact Mixing and flow is an important factor in the design of spray drier. The product and air flow into the dryer can be designed in co-current, counter-current or mixed flow patterns. Sine heat sensitive product is […]
Feb 29 2012 | Posted in
Business |
Read More »
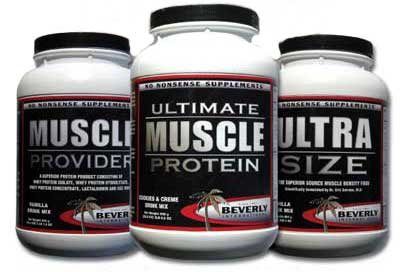
Designing of the dryer section of nutritional yeast production plant – Industrial sector review – Part 18 Feed cream is introduced centrally on to a wheel rotating at speed of 10 000 r.p.m. The feed flows outwards over the surface, accelerating to the outer boundary of the atomizer. The cream on leaving the atomizer readily […]
Feb 29 2012 | Posted in
Sci-Tech |
Read More »
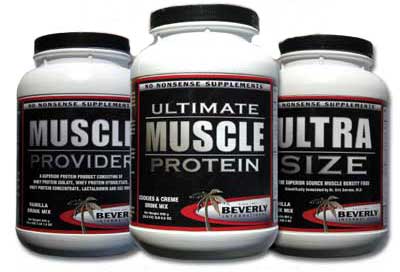
Designing of the dryer section of nutritional yeast production plant – Industrial sector review – Part 17 Atomization of feed It is necessary to dispense and distribute the cream under control conditions, which is done by the atomizer. Generally the atomizers are divided into two sub division, namely (1) Rotary and (2) Nozzle atomizers. The […]
Feb 29 2012 | Posted in
Sci-Tech |
Read More »
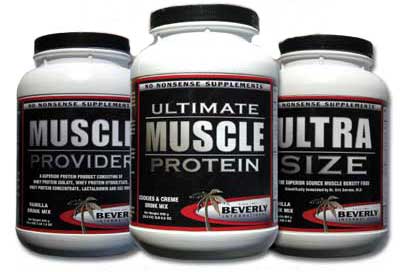
Designing of the dryer section of nutritional yeast production plant – Industrial sector review – Part 16 PROCESS DESCRIPTION In this section, details of the mass and energy balances along with the drying process description are detailed. Introduction Yeast broth from the fermentor is delivered to separator which produces a thick suspension of yeast (cream). […]
Feb 29 2012 | Posted in
Sci-Tech |
Read More »
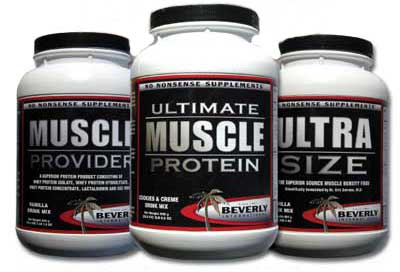
Designing of the dryer section of nutritional yeast production plant – Industrial sector review – Part 15 For the cycle of the air, please see attached Psychometric charts Saturated Wet bulb temperature of the Air = 55 °C (after heating to 300 °C) Drying Air Mass flow rate = 20,685 kg/hr Drying Air Volumetric Flow […]
Feb 29 2012 | Posted in
Sci-Tech |
Read More »
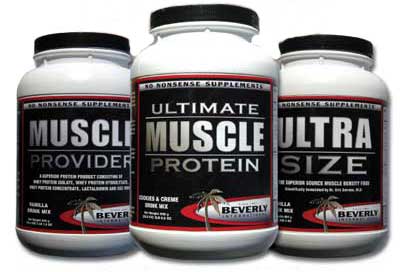
Designing of the dryer section of nutritional yeast production plant – Industrial sector review – Part 14 Using this efficiency, the total product loss is calculated as 0.06 x 348.5 = 2.091 k/hr, which equals 16560 kg/year (plant running for 330 days). The product is sold at £10/kg, which also includes further processing costs which […]
Feb 29 2012 | Posted in
Sci-Tech |
Read More »
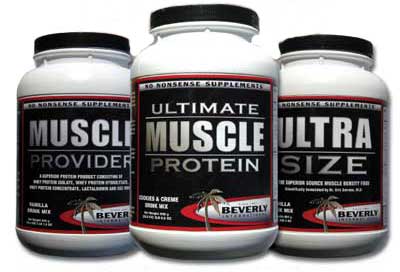
Designing of the dryer section of nutritional yeast production plant – Industrial sector review – Part 13 Using this efficiency, the total product loss is calculated as 0.06 x 348.5 = 2.091 k/hr, which equals 16560 kg/year (plant running for 330 days). The product is sold at £10/kg, which also includes further processing costs which […]
Feb 29 2012 | Posted in
Sci-Tech |
Read More »